Case Studies
Redrow Homes
Sites throughout the UK.
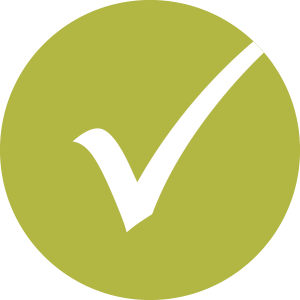
The use of Hi-therm+ provided Redrow with an average saving of £200 per plot.
“By including low psi value Hi-therm+ Lintels into our group specification, the improved performance within SAP calculations allowed us to achieve overall significant cost savings by reviewing the ground floor insulation specification whilst still meeting the requirements of Part L Regulations.
The Hi-therm+ lintel has proven to be a cost effective solution to tackle concentrated areas of heat loss and contribute to the energy performance of our group house type range.”
Jonathan Moss
Group Technical Manager, Redrow Homes Ltd
Hi-therm+ Solution
-
By switching from standard lintels to Hi-therm+ lintels. Redrow Homes benefited from improved thermal performance, helping them to meet SAP requirements without the need for additional insulation.
-
The use of Hi-therm saved Redrow Homes an average of £200 per plot.
-
Based on an average of 5,800 plots built by Redrow last year that could equate to a yearly saving of £1,160,000.
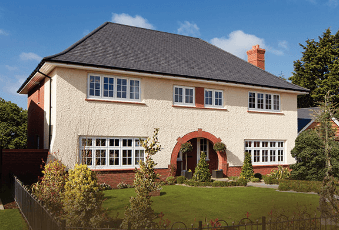
Project Details
-
Redrow Homes build an average of 5,800 plots a year, by switching all their new developments to Hi-therm+ they were able to achieve their SAP requirements in the most cost effective way, removing the need for additional bolt on technologies.
New Barratt Homes
Sites throughout the UK.
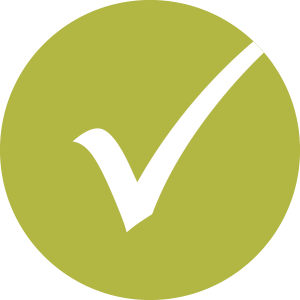
Specifying Hi-therm significantly reduced thermal bridging on all house types.
“ When the government unveiled its changes to Part L 2013 building regulations Barratts analysed a range of sustainable solutions in order to comply with the mandatory minimum fabric performance standard (Target Fabric Energy Efficiency, TFEE). The Hi-therm lintel has proved to offer a cost effective option as part of a suite of specification upgrades. ”
Michael Finn
Group Design & Technical Director
Barratt Homes
Hi-therm Solution
-
Full technical support and site-specific Psi value calculations provided.
-
Hi-therm significantly reduces the thermal bridging through window & door head junctions to achieve class leading values.
-
Hi-therm lintels are single piece and fitted in the same method as a standard steel lintel, so require no special arrangements on-site.
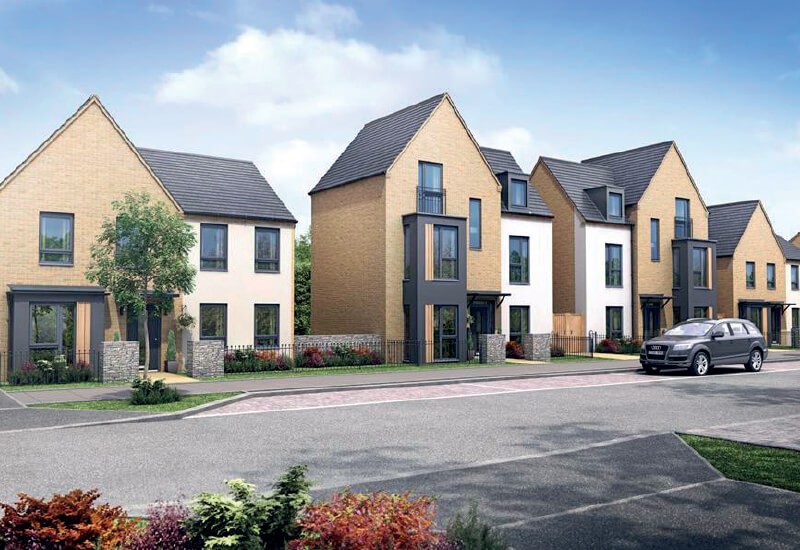
Project Details
-
Barratts are required to meet the increased performance demands on plots which must comply with part L 2013.
Oakgrove Village
Milton Keynes, Buckinghamshire.
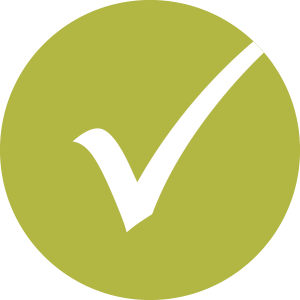
Specifying Hi-therm significantly reduced thermal bridging on all house types.
“ We specified Hi-therm lintels on our Oakgrove development in Milton Keynes where we are required to meet Level 4 of the CfSH. Crest Nicholson traditionally take the approach of achieving the carbon and energy saving required on a development through a fabric first approach and the Hi-therm lintel contributes to this approach by significantly reducing the thermal bridging through the window and door head junction, making it a cost effective option on this Code 4 site. ”
Darren Dancey
Group Technical & Quality Director
Crest Nicholson
Hi-therm Solution
-
Full technical support and site-specific Psi value calculations provided.
-
Hi-therm significantly reduced the thermal bridging through all window & door head junctions across all house types in the development.
-
Hi-therm lintels are fitted in the same method as a standard steel lintel, so had no impact on the construction sequencing.
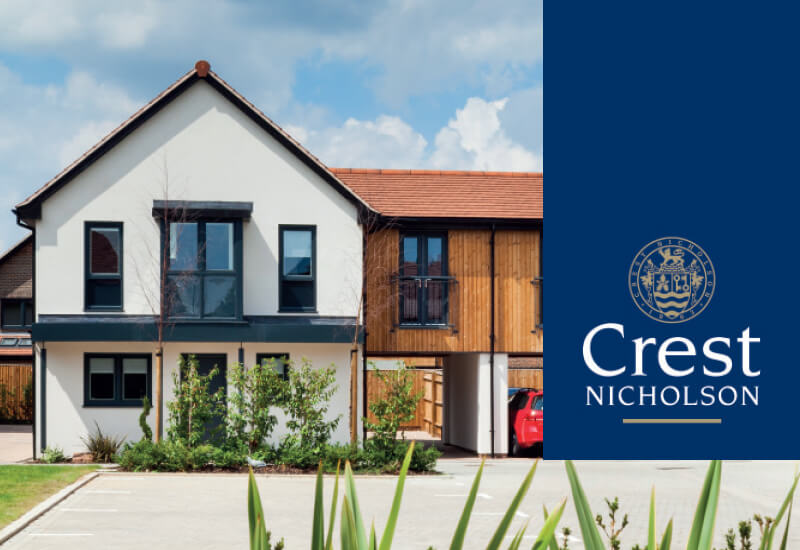
Project Details
-
Crest Nicholson were required to build all house types on their Oakgrove Village development to meet Level 4 of the Code for Sustainable Housing.
Gospel Oak
Tipton, West Midlands.
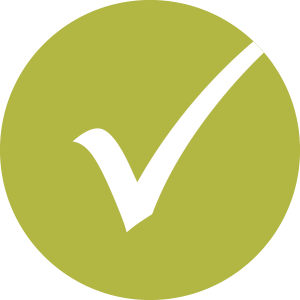
Hi-therm saved more than £200 per plot and dramatically improved the fabric performance without any specialist build techniques.
“ As an experienced builder of eco-friendly homes, we were very impressed with the innovation of the Hi-therm lintel’s fabric first approach. With the new Part L 2013 regulations tightening we are always looking for cost effective solutions to improving the building’s overall thermal performance. No other single lintel product has enabled us to reduce thermal bridging as much as Hi-therm. This fabric first approach has enabled us meet the new regulations without the need for costly renewable technology or wider cavities. ”
Richard Southgate
Project Co-ordinator/Owner
Wrekin Eco Homes
Hi-therm Solution
-
The use of Hi-therm saved more than £200 per plot by enabling the use of a 100mm cavity instead of a 125mm width.
-
Hi-therm dramatically improved the fabric performance without any additional or specialist build techniques.
-
Hi-therm does not require any of the maintenance associated with many other sustainable technologies.
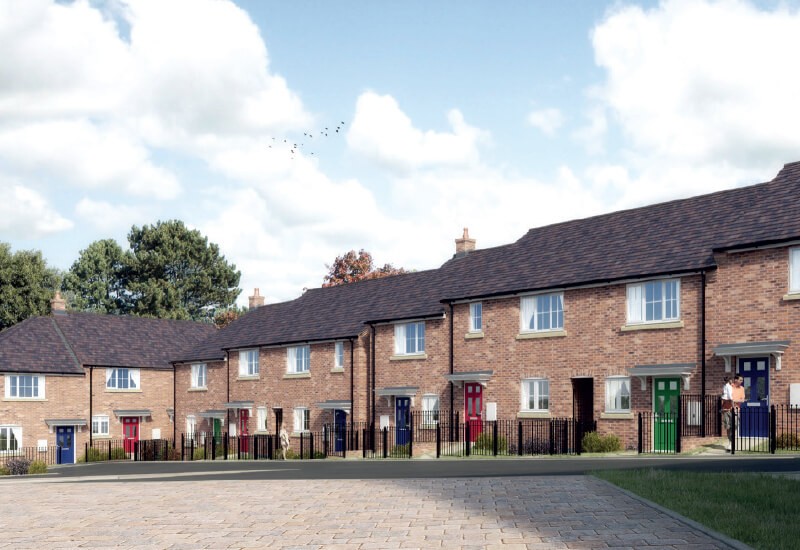
Project Details
-
Wrekin Homes purchased the site to develop Eco Homes in Tipton, West Midlands.
-
Wrekin sought out the latest fabric first solutions.
Coxon’s Mews
Ashby-De-La-Zouch, Leicestershire.
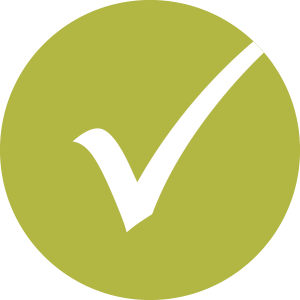
The use of Hi-therm saved £1000’s by negating the use of costly alternatives.
“When split lintels were specified for this project I looked for an alternative product to avoid the increased handling and site work they would involve. Ashby Energy, our energy assessor, introduced the Hi-therm lintel which significantly lowered the amount of thermal bridging, helping us to meet level 4 in the code for sustainable homes with the simple installation of single piece lintels. ”
Frank Sandkey
Buyer
Lychgate Homes
Hi-therm Solution
-
By using Hi-therm as a fabric first solution, thermal bridging was significantly reduced enabling the energy target to be met without the use of wider cavities or PV units.
-
The use of Hi-therm saved £1000’s by negating the use of the costly alternatives.
-
Hi-therm was simple to install, avoiding the complexity of split lintels.
-
No ongoing maintenance required.
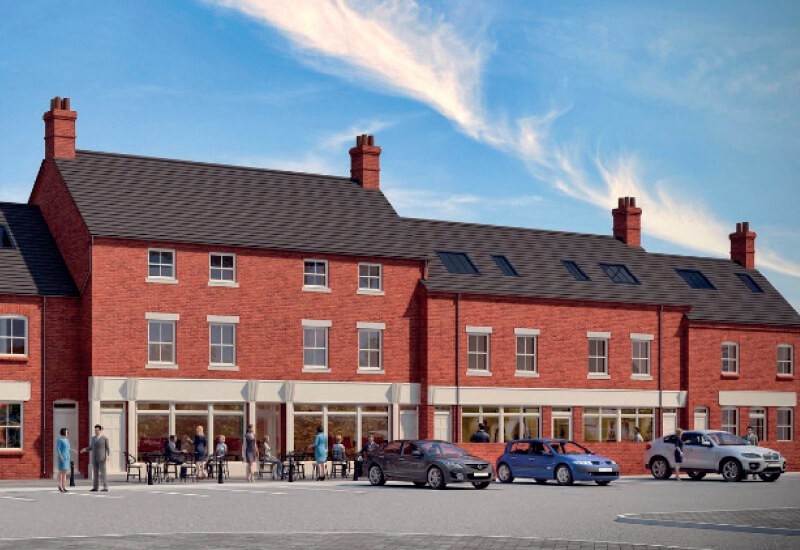
Project Details
-
The planning approval for 4 retail units and 7 duplex apartments required Level 4 Code for sustainable homes performance.
-
Design options included either 125mm Cavity or the use of PV panels to meet Level 4 energy/CO2 targets.
Berewood
Waterlooville, Hampshire.
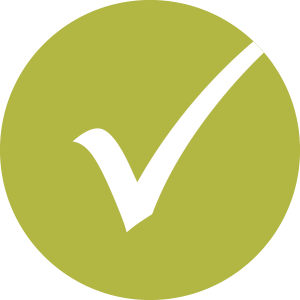
The use of Hi-therm saved £1,000’s by negating the use of costly alternatives.
“The Waterlooville site was required to meet Level 4 of the code for sustainable homes. We wanted to achieve compliance and deliver the energy savings with a cost effective fabric first approach rather than the use of complex and expensive renewable technologies. Having discussed this with our energy assessor and our lintel supplier we decided to specify the Hi-therm lintel. This choice delivered reduced thermal bridging at the head junctions and openings allowing us to meet our carbon targets. We particularly valued the fact that no changes to our construction practices on-site were required.”
Phil Jackson
Group R&D Manager
Bloor Homes
Hi-therm Solution
-
The use of Hi-therm was a significant contributor to the achievement of Level 4, Code for sustainable homes.
-
Full technical support provided to develop a suitable specification for the site.
-
Hi-therm does not require any special installation techniques.
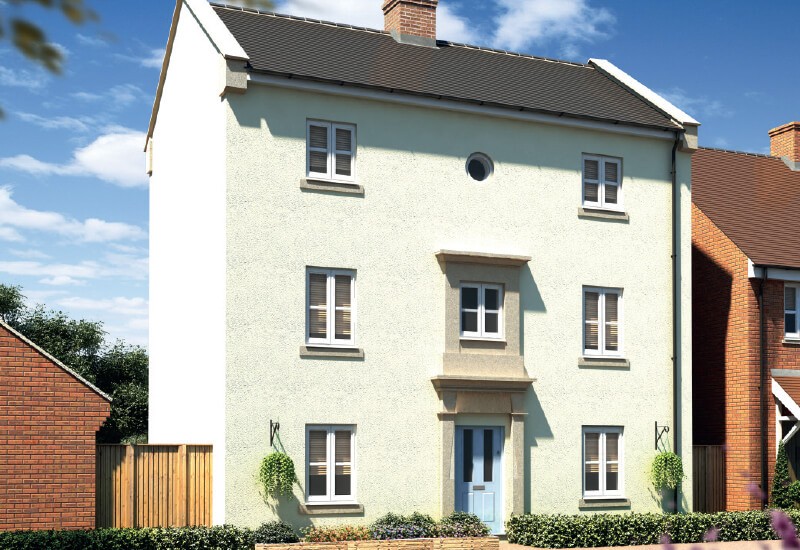
Project Details
-
The Berewood development includes a full range of property types from 1 to 5 bedrooms and Hi-therm was specified on each home within the 168 acre site.
St. Inns
Moira, Co. Armagh.
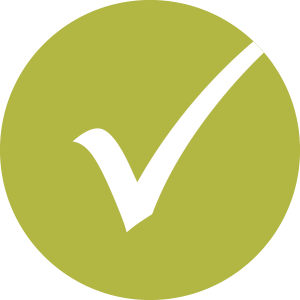
The use of Hi-therm contributed savings of more than £1000 per plot on other technology.
“ Using the Hi-therm lintel helped us to achieve a pass rating keeping the air test above 5, therefore removing the need for mechanical whole house ventilation/heat recovery, or alternatively other renewable energy products such as PV. Whilst the Hi-therm was not the only resolution, it is a combination of various products and u-values etc. which achieve the pass; Hi-therm helped to achieve the pass in this instance. ”
Chris Carroll
Quantity Surveyor
Lagan Homes
Hi-therm Solution
-
Full technical support and site-specific Psi value calculations provided.
-
Hi-therm’s performance contributed to the saving of upwards of £1000 per plot on other sustainable technology.
-
Hi-therm does not require any ongoing maintenance, unlike many alternative sustainability solutions.
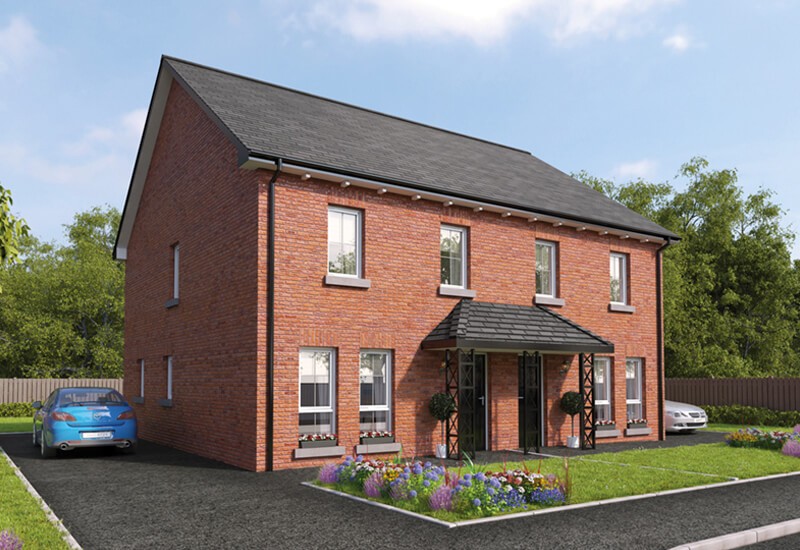
Project Details
-
St. Inns development at Moira, Co. Down, includes detached and semi-detached 3 and 4 bedroom house types and Hi-therm was specified on each home.
Martello Park
Felixstowe, Suffolk.
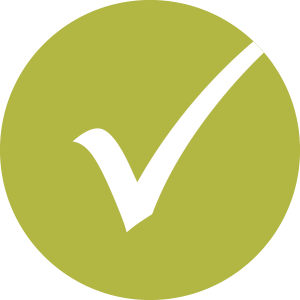
Coastal regions require enhanced specification and the corrosion proof Hi-therm lintel was ideal.
“The Felixstowe seafront site had to be built to the enhanced standards required to withstand coastal conditions. This traditionally includes the use of stainless steel lintels to prevent corrosion. However we specified the innovative new Hi-therm lintel with its corrosion proof GRP outer leaf which is NHBC approved for use in coastal areas. We liked the way that Hi-therm builds like a normal steel lintel but also delivers considerable improvements in SAP, delivering an overall cost effective specification. ”
Phil Jackson
Group R&D Manager
Bloor Homes
Hi-therm Solution
-
The use of Hi-therm was a more efficient solution than stainless steel lintels and was NHBC compliant.
-
Hi-therm also dramatically improved the fabric energy performance compared to the use of stainless steel lintels.
-
Hi-therm does not require any specialinstallation techniques.
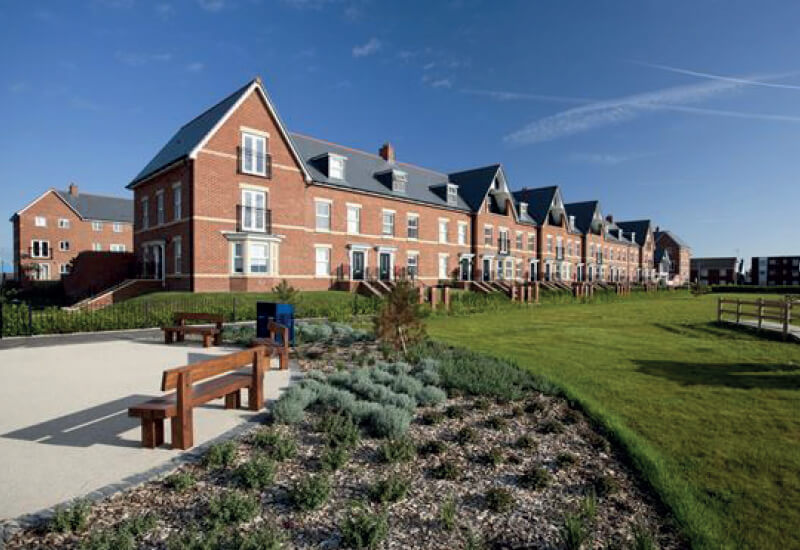
Project Details
-
This popular seafront location contains a range of house types.
-
Coastal locations require the use of NHBC approved corrosion resistant lintels.
Saxon Place
Penwortham, Lancashire.
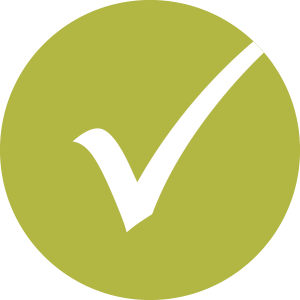
The use of Hi-therm sustainability lintel saved over £300 per plot on wall insulation.
“ At Rowland we aim to build a better home for our house buyers which will lower their energy costs and minimise maintenance. That’s why we were so impressed by what the Hi-therm lintel offered us in terms of thermal performance while at the same time being extremely cost effective to build. ”
Scott Warley
Senior Buyer
Rowland Homes
Hi-therm Solution
-
By utilizing Hi-therm’s thermal performance and enhanced psi value, Rowland was able to re-assess the overall fabric specification.
-
The use of Hi-therm saved over £300 per plot by enabling the wall insulation cost to be reduced from 0.32w/m/h to 0.36w/m/h.
-
Hi-therm was specified on all house types within the development, providing £1,000’s of savings overall.
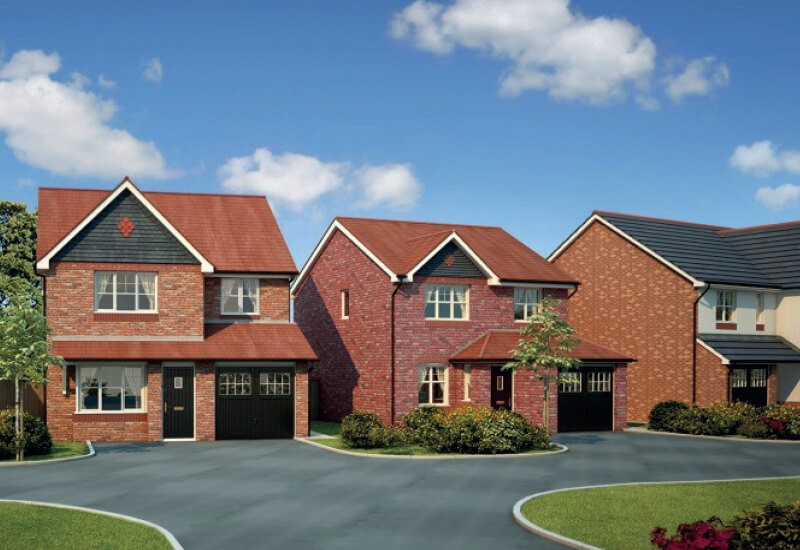
Project Details
-
This is a quality development of 61, 3 and 4 bedroom houses in a scheme, designed and landscaped to create a mature, established feel.
-
Rowland are committed to building environmentally efficient homes using the latest sustainable technologies.
New Jelson Homes
Sites throughout the UK.
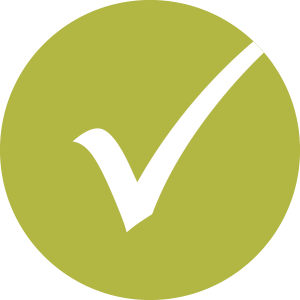
The use of Hi-therm saved up to £400 per plot on PV panels.
When introduced to Hi-therm, Jelson’s energy assessors discovered they could considerably enhance the energy performance of the houses by adopting the use of Hi-therm in all their house types. The increase in performance was so substantial that it enabled the assessors to still meet the building codes while removing one to two PV panels per plot at a saving of £350 – £400 per panel.
As a result of these cost efficiencies, Jelson now include Hi-therm sustainability lintels in the specification of all new builds going forward.
Additional Issues
-
Unlike other sustainability technologies, Hi-therm lintel does not require any ongoing maintenance throughout the life of the building.
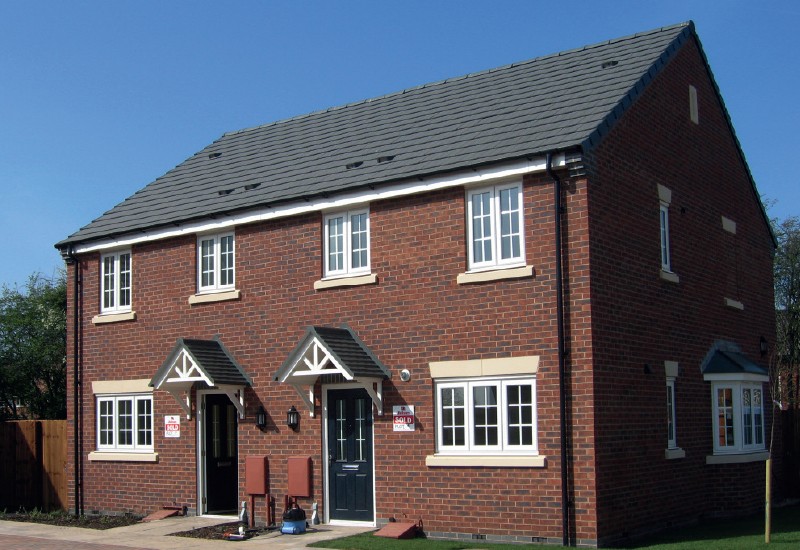
Project Details
-
To meet the required codes and building regulations for their standard house type, Jelson Homes had adopted a specification requiring a 100mm cavity and the use of PV panels to enhance their energy performance.
New Developments
East Riding PHASE 4 Housing.
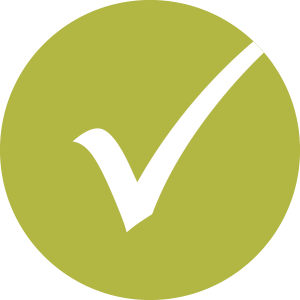
Solved site issues and helped them meet thermal bridging requirements.
“Within the Building Design department of East Riding of Yorkshire Council we are constantly looking at products which will enhance the quality and performance of our buildings. We were specifying a split lintel solution with 150mm wide cavities for our affordable housing developments to help lower thermal bridging and meet building regulations.
Unlike other sustainability technologies, Hi-therm lintel does not require any ongoing maintenance throughout the life of the building. However, the split lintel option was causing installation issues on site with the insulation and DPC detail around the split lintels and therefore were looking for a solution to ease the installation and maintain the thermal insulation continuity.
We were introduced to the Hi-therm Lintel which our technical team and Energy Assessor recognised would offer benefits over split lintels from a technical and building construction perspective. As a result, we have now specified the Hi-therm Lintel for our next phase of affordable homes.”
Mark Thomas
Senior Architect,
ERI&F Building Design
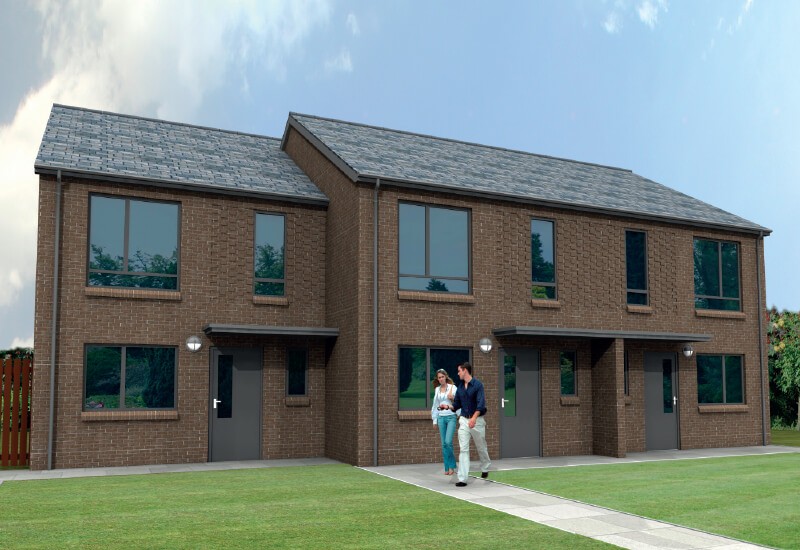